Imagine walking into a factory that produces zero waste, emits minimal greenhouse gases, and runs entirely on renewable energy. Sounds almost too good to be true, doesn’t it? Yet, this is the direction many businesses are heading, and it’s a transformation that couldn’t come at a more crucial time. Climate change, resource depletion, and environmental degradation are no longer distant problems—they’re challenges staring us in the face. In response, companies worldwide are rethinking how they make products, and green manufacturing is leading the charge.
Green manufacturing is more than just a buzzword; it’s a movement reshaping industries. It’s about creating products in a way that minimises harm to the planet, from reducing waste and emissions to using sustainable materials and energy sources. Why does this matter? Because every choice we make—from how we produce goods to what we consume—has a ripple effect on the environment.
In this guide, I’ll walk you through what green manufacturing really means, why it’s so important, and how businesses can embrace it. Through real-world stories, research-backed insights, and practical advice, you’ll discover how innovation and sustainability can go hand in hand to shape a better future for us all.
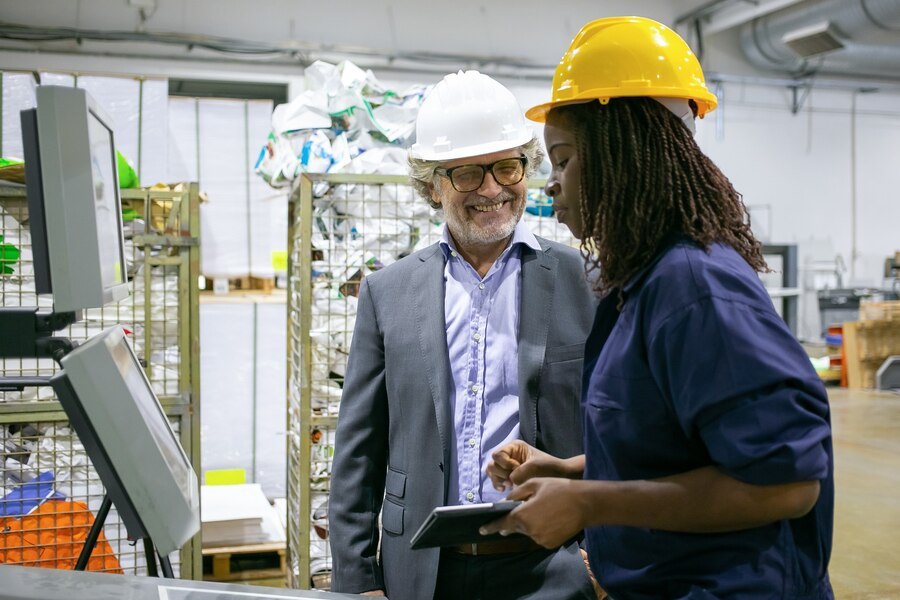
In This Article
- What Is Green Manufacturing?
- Why Does Green Manufacturing Matter?
- Real-World Examples of Green Manufacturing
- How to Transition to Green Manufacturing
- Innovations Driving Green Manufacturing
- Challenges and Solutions in Green Manufacturing
- The Future of Green Manufacturing
- Actionable Advice for Businesses
- Conclusion
- References:
What Is Green Manufacturing?
Green manufacturing is about doing business while respecting the planet. It’s a way of making things—products we use every day—in a manner that minimises harm to the environment. This approach isn’t just about following rules; it’s about actively choosing to care for the world we live in. Think of it as creating something with a lighter footprint—using fewer resources, generating less waste, and thinking ahead about how to keep materials in use rather than throwing them away.
Let’s break it down into some core principles:
- Resource Efficiency: This means using raw materials and energy as effectively as possible. For example, imagine a factory that uses software to track and cut down on energy waste, or a company that sources its materials locally to reduce transportation emissions.
- Waste Reduction: Here, it’s all about the 3 R’s: reduce, reuse, and recycle. Manufacturers can design products in a way that generates less waste during production and encourages recycling at the end of the product’s life.
- Carbon Neutrality: Many manufacturers are working toward net-zero carbon emissions by adopting renewable energy sources like solar or wind, or by offsetting their emissions through projects like tree planting.
- Eco-Friendly Materials: Using materials that are biodegradable or recyclable helps prevent harm to the environment. For instance, replacing plastic packaging with compostable alternatives makes a big difference.
- Circular Economy Practices: This principle focuses on designing products that can be easily repaired, reused, or recycled. Think of a company that builds laptops where every part can be swapped out instead of throwing the whole device away.
Why Does Green Manufacturing Matter?
The manufacturing industry has a significant impact on the planet. According to the International Energy Agency (IEA), it contributes about 30% of global greenhouse gas emissions. That’s a big number. When you consider how much manufacturing contributes to pollution and resource depletion, it’s clear why shifting to greener practices is not just helpful—it’s necessary.
Dr. Susan Miller, an environmental activist, puts it perfectly: “Green manufacturing is not just an ethical choice; it’s a business imperative. Sustainable practices reduce costs, improve brand reputation, and meet the demands of conscious consumers.”
But what does this mean for us as individuals? Let’s bring it closer to home.
When companies prioritise green manufacturing, the products we use daily—whether it’s the phone in your pocket, the clothes you wear, or the food packaging in your pantry—come with a smaller environmental cost. It’s like choosing a product that doesn’t just work for you but works for the planet, too.
Real Benefits of Green Manufacturing
The advantages of green manufacturing ripple outwards. Here are some of the key benefits:
- Protecting the Environment: By reducing pollution, conserving natural resources, and producing less waste, green manufacturing directly combats environmental degradation. For example, a factory that recycles water instead of discharging it into local rivers prevents contamination and saves water resources.
- Economic Gains: Many companies find that adopting green practices saves money in the long run. Energy-efficient equipment can cut power bills, and reducing waste means spending less on disposal. It’s a win-win situation—less cost, less waste.
- Attracting Consumers: Today’s shoppers are more aware than ever. People want to support brands that care about the planet. Choosing green manufacturing can make a company stand out and build loyalty with eco-conscious customers.
- Regulatory Compliance: Environmental regulations are becoming stricter around the world. Companies that embrace green practices now are better positioned to meet these rules and avoid costly fines later.
Learn More: When did Sustainability Become Popular in Business?
Real-World Examples of Green Manufacturing
1. Tesla’s Gigafactories: Powered by the Sun and Wind
When you hear “Tesla,” you probably think of electric cars, but there’s more to the story. Tesla’s Gigafactories are the backbone of their mission to accelerate the world’s transition to sustainable energy. These massive facilities are powered by renewable energy sources like solar and wind, which means the cars rolling off the assembly line are created with as little environmental impact as possible.
Here’s a standout achievement: In 2022, Tesla reported a 15% reduction in manufacturing energy use per vehicle compared to the previous year. That’s not just a small tweak; it’s a significant shift that shows how a commitment to sustainability can lead to tangible results. By designing their factories to use renewable energy and operate efficiently, Tesla is setting a powerful example for other manufacturers.
2. Interface Carpets: Flooring That Doesn’t Cost the Earth
Interface, a global leader in flooring, might not seem like a company that’s making waves in sustainability, but they’ve been quietly revolutionising their industry for decades. Their “Mission Zero” initiative aimed to eliminate their environmental footprint by 2020, and they came astonishingly close to achieving that goal.
How did they do it? Interface shifted to using recycled materials for their carpets, reducing the demand for virgin resources. They also power their operations with renewable energy, cutting down on carbon emissions. Since 1996, Interface has slashed its greenhouse gas emissions by a whopping 96%. Imagine that: nearly eliminating their contribution to climate change over just a few decades.
This transformation wasn’t easy or cheap, but it’s paid off in more ways than one. Customers now see Interface as a pioneer in green manufacturing, and the company has built a loyal following of environmentally conscious buyers. It’s proof that doing the right thing for the planet can also be good for business.
3. Unilever’s Sustainable Factories: Zero Waste, Big Impact
Unilever, the company behind household brands like Dove, Ben & Jerry’s, and Lipton, has been making big moves toward sustainability. One of their standout achievements is transitioning several of their factories to zero waste-to-landfill operations. What does that mean? Essentially, they’ve found innovative ways to ensure that almost nothing from these facilities ends up in a landfill.
In 2021, Unilever managed to divert over 99% of its waste from landfills. They’ve done this by rethinking their waste management systems—from recycling and reusing materials to finding creative ways to handle byproducts. For example, some waste materials are turned into compost or used as fuel. This approach doesn’t just reduce landfill contributions; it also saves money and resources.
What makes Unilever’s story so compelling is its scale. They’re not a niche company; they’re a global giant. If they can make these kinds of changes across their operations, it’s a hopeful sign that other large corporations can follow suit.
Putting It All Together
To sum it up, here’s a snapshot of these companies’ green practices and their impact:
Company | Green Practice | Impact |
---|---|---|
Tesla | Renewable energy in factories | 15% reduction in energy use per unit |
Interface | Recycled materials | 96% emission reduction since 1996 |
Unilever | Zero waste to landfill | 99% waste diversion |
How to Transition to Green Manufacturing
Transitioning to green manufacturing is not just about adopting eco-friendly practices—it’s about rethinking how we approach production, innovation, and sustainability as a whole. The process requires strategy, commitment, and a willingness to embrace new technologies and mindsets. Here’s how businesses can embark on this transformative journey.
1. Conduct an Environmental Audit
The first step to transitioning is understanding where you stand. Conducting an environmental audit helps identify inefficiencies and areas where your processes are causing the most harm.
Personal Insight: When I collaborated with a medium-sized textile company, we conducted an energy audit that revealed a surprising statistic: their outdated machinery was responsible for 40% of their energy consumption. I remember the CEO’s shock when the report came in. But this wasn’t just a wake-up call—it became a turning point. Upgrading to energy-efficient models not only reduced their carbon footprint but also saved the company $50,000 annually in energy costs.
Pro Tip: Look beyond machinery. Assess water usage, waste production, and supply chain efficiency as well. Tools like the ISO 14001 standard provide a comprehensive framework for environmental management systems.
2. Invest in Renewable Energy
Switching to renewable energy sources like solar, wind, or geothermal power can drastically cut your operational carbon footprint. While the upfront costs can be high, the long-term savings and environmental benefits are undeniable.
Real-World Example: IKEA’s commitment to sustainability offers a powerful example. In 2023, they installed solar panels across their manufacturing facilities, generating an impressive 1.7 terawatt-hours of renewable energy. That’s enough to power over 400,000 homes for a year. The move didn’t just enhance their brand’s green credentials—it demonstrated that even global giants can embrace sustainability without compromising profitability.
Actionable Tip: Explore government incentives and grants for renewable energy projects. In many countries, businesses can offset initial costs with subsidies.
3. Adopt Lean Manufacturing Practices
Lean manufacturing focuses on minimising waste while maximising productivity. It’s an approach that aligns perfectly with green manufacturing goals.
Key Principles:
- Just-In-Time (JIT) Production: Reduces overproduction and excess inventory.
- Kaizen (Continuous Improvement): Encourages small, incremental changes that add up to significant environmental benefits.
For instance, a furniture company that embraced lean principles reduced material waste by 30% simply by streamlining its production process and improving demand forecasting.
4. Embrace Circular Economy Practices
A circular economy approach involves designing products with their entire lifecycle in mind. This means creating items that can be easily disassembled, repaired, or recycled, reducing reliance on virgin materials.
Example: Patagonia, the outdoor clothing brand, is a leader in this space. Their Worn Wear initiative encourages customers to repair and reuse clothing rather than buy new items. By focusing on durability and recyclability, they’ve built a business model that’s both profitable and sustainable.
Actionable Tip: Start small. Introduce a take-back program where customers can return used products for recycling or refurbishing.
5. Employee Training and Engagement
No sustainability initiative can succeed without the support and involvement of employees. From top management to factory workers, everyone needs to understand their role in the transition.
Case Study: A manufacturing firm I worked with launched a series of sustainability workshops for their staff. They covered topics like energy-saving practices and waste reduction. To motivate employees further, they introduced a rewards program for green ideas. Within a year, employee-driven suggestions reduced waste by 20% and cut energy use by 15%.
Pro Tip: Communication is key. Share your sustainability goals and progress with employees regularly to keep them engaged and inspired.
Learn More: What Does Sustainably Sourced Mean? An Expert Guide
Innovations Driving Green Manufacturing
1. 3D Printing
3D printing, also known as additive manufacturing, reduces material waste by creating products layer by layer instead of cutting from larger blocks. This method can cut material usage by up to 90% compared to traditional methods.
Real-World Application: Custom medical implants created through 3D printing have not only minimised waste but also improved patient outcomes by offering personalised solutions.
2. Artificial Intelligence (AI)
AI is revolutionising manufacturing by optimising production processes, predicting maintenance needs, and reducing energy consumption.
Example: Siemens’ AI-driven factories saved 15% in energy costs in 2022. Their advanced algorithms analyse production data in real-time, ensuring machines operate at peak efficiency.
Actionable Tip: Consider investing in AI-powered tools that monitor energy usage and predict maintenance schedules. These tools often pay for themselves within a few years.
3. Biodegradable Materials
Innovations in materials science have led to the development of bio-based plastics and other biodegradable materials that offer sustainable alternatives to traditional plastics.
Example: A packaging company switched to bio-based plastics for their products, cutting down plastic waste by 70%. These materials decompose naturally, reducing environmental impact.
Research Table
Innovation | Benefit | Example |
---|---|---|
3D Printing | Reduces material waste | Custom medical implants |
Artificial Intelligence | Optimizes energy use | Siemens’ smart factories |
Biodegradable Materials | Eco-friendly product alternatives | Bio-based packaging |
Challenges and Solutions in Green Manufacturing
1. High Initial Costs
Let’s face it—going green isn’t cheap, at least not at the start. Installing solar panels, switching to energy-efficient machinery, or reworking supply chains to incorporate sustainable materials often involves significant upfront expenses. For example, replacing an old industrial furnace with a newer, energy-efficient model can cost tens or even hundreds of thousands of dollars.
This cost is a huge hurdle, especially for smaller companies operating on tight margins. However, businesses that take the leap often discover that these investments pay for themselves over time. Energy-efficient equipment reduces electricity bills, and waste reduction initiatives lower disposal costs. A manufacturing plant in California, for instance, reported saving over $200,000 annually after installing a water recycling system—a hefty saving that made the initial expense worth it.
Solution: Start Small and Seek Support
If the cost feels overwhelming, start small. Replace old lighting with LED bulbs or install motion sensors to cut energy use in less-used areas. Governments and organisations also offer financial incentives. In the U.S., programs like the Federal Investment Tax Credit (ITC) provide significant tax breaks for renewable energy investments, helping to offset those high upfront costs. Don’t hesitate to tap into these resources—they’re there to help businesses like yours succeed.
2. Supply Chain Complexity
Have you ever tried sourcing eco-friendly materials? It’s not always as straightforward as it seems. Many manufacturers face difficulties finding reliable suppliers who meet sustainability standards. And even when you do find them, the costs can be higher, and logistics more complicated.
A friend of mine, who runs a small clothing brand, shared her struggle with sourcing organic cotton. She found a supplier in India but faced delays due to shipping challenges and miscommunications. On top of that, the cost of organic cotton was nearly double that of conventional options, putting pressure on her budget.
Solution: Build Strong Relationships
The key to tackling supply chain issues is building solid partnerships. Look for suppliers who share your sustainability goals and can commit to consistent quality. My friend eventually partnered with a supplier who not only provided organic cotton but also offered bulk discounts. Joining sustainability-focused industry groups can also help you connect with like-minded businesses and share resources.
3. Technological Barriers
New technologies like automation, AI, and advanced recycling systems are driving green manufacturing forward. But adopting these innovations often requires expertise that many businesses lack. For example, implementing an AI-driven energy monitoring system might sound great, but without trained staff, it’s just an expensive piece of equipment gathering dust.
Solution: Invest in Training
Investing in employee training is non-negotiable. Businesses need to upskill their workforce to stay competitive. Many companies have successfully addressed this by partnering with local technical colleges or offering on-the-job training programs. These initiatives ensure employees are equipped to use the latest technologies effectively, turning barriers into opportunities.
Learn More: 20 Best Eco-Friendly Activities to Help Your Environment
The Future of Green Manufacturing
Green manufacturing isn’t a niche trend—it’s the future. By 2030, the global green manufacturing market is expected to be worth a staggering $1.6 trillion, thanks to advances in renewable energy, government incentives, and growing consumer demand for eco-friendly products.
But beyond the numbers, the future of green manufacturing is about more than profits. It’s about creating a world where businesses and the environment thrive together. Imagine factories powered entirely by renewable energy, with zero waste and fully recyclable products—that’s the vision we’re working towards.
Actionable Advice for Businesses
If you’re considering green manufacturing but aren’t sure where to start, here are some simple, actionable steps:
- Start Small: You don’t have to overhaul your entire operation overnight. Begin with manageable changes like switching to energy-efficient lighting or implementing a recycling program.
- Leverage Government Incentives: Research subsidies, grants, and tax breaks for green initiatives. For example, many countries offer financial incentives for renewable energy adoption or waste management upgrades.
- Monitor and Adapt: Track your progress using Key Performance Indicators (KPIs). Whether it’s energy usage, waste reduction, or cost savings, measuring results helps you adapt and improve.
- Collaborate: Don’t go it alone. Partner with other businesses, join sustainability-focused networks, or collaborate with local organisations to share resources and expertise.
Conclusion
Green manufacturing is not just an ethical choice; it’s a pathway to innovation, resilience, and profitability. By embracing sustainable practices, businesses can protect the planet while thriving in a competitive market. Let’s take action today to build a sustainable tomorrow.